We are currently working on a project that is utilizing a ground sourced Geo-Thermal Heat Pump HVAC system.
I am a big fan of these systems as they are unmatched for efficiency of operation. Geo systems are about 400% efficient as compared to the best LP systems which are about 95% efficient. In other words, for every dollar of energy purchased to operate the system (electricity for a Geo system) a Geo-Thermal system delivers four dollars worth of heat (the LP system delivers .95 cents worth of heat for every dollar of LP purchased)!
This system was designed and installed by Elco Geo-Thermal Heating of Bangor ME.
It is an "Open Loop" system which utilizes the existing domestic supply well for its heat exchange source. Simply, water from the well is pumped to the heat pump, heat is extracted from the water, and then it is returned to the well.
The system delivers heat and air-conditioning via a ducted forced air delivery.
As an added benefit, whenever the system is operating it also pre-heats domestic supply water as a free by-product which is then held in a storage tank until required which further reduces energy costs.
We have also added a Heat Recovery Ventilation (HRV) system which works in concert with the HVAC system to provide a continuous fresh air exchange into the building envelope while capturing much of the heat from the exhaust air being removed from the house.
These systems do cost more than typical Oil or LP boiler/furnace systems, however they currently enjoy a 30% Federal Tax Credit (through 2016) which makes the installed price very competitive and the return on investment time relatively short.
I am a big fan of these systems and we are specifying them in several upcoming projects, including our own home!
Saturday, December 10, 2011
Monday, August 15, 2011
Energy efficient construction
No matter what house style, no matter what budget, energy efficient building techniques should be utilized to enhance ongoing home energy performance.
The following photographs of a current project in New Gloucester Maine highlight a few details that will have a dramatic positive effect regarding how comfortable this house will be, as well as less expensive to heat.
The following photographs of a current project in New Gloucester Maine highlight a few details that will have a dramatic positive effect regarding how comfortable this house will be, as well as less expensive to heat.
Intersecting wall framing techniques that allow full insulation to be installed in the outside wall cavity which eliminates an area of potential thermal transfer from conditioned to unconditioned space
Insulated window and door header assemblies with continuous rigid foam insulation
Wall corner construction that allows our blown in insulation to fully insulate this often neglected area
Even though we utilize foam sill seal gasket between the sill plate and foundation wall,
we also caulk this seam with silicon caulk
We will foam seal all sheathing panel edges as well as both sides of any wall stud where two panels meet and at the top and bottom plate
It only takes advanced planning, a little extra time and a few cans of DOW Pro foam to make a big difference.
Tuesday, May 24, 2011
Build new houses tight, tight, tight!
I sometimes hear people say things like "new houses today are being built too tight".
I might share this opinion if I were a home heating fuel salesman, but as a Maine home builder with a focus on saving my customers money through energy efficient construction, I say that it is better to understand building science, specifically moisture management, and build new homes as tight as you are able.
Years ago, fuel costs were low, and moisture management not well understood. Houses that leaked air were not much of a concern. They would get wet, but with an abundance of air moving through the walls would dry avoiding moisture damaged assemblies.
With rising fuel costs houses had to become better insulated and tighter, and fortunately within the past decade or so, building science case studies have shown new home builders the way to build structures that are not only tight, but also properly manage bulk moisture from external sources and moisture vapor from internal sources.
Today's home builders are fortunate to have the availability of a wide variety of excellent building products as well as the educational resources to build new homes that are both energy efficient and sustainable.
Products such as "Greenguard Raindrop house wrap" which facilitates a drainage plane between exterior cladding and wall sheathing, "Advantech" brand roof and wall sheathing which is highly resistant to moisture damage, "DOW" "SIS Structural Insulated Sheathing", "Styrofoam" extruded insulation panels, and "Thermax" insulation panels, "DOW" "Weathermate" construction tape and "DOW" "Great Stuff Pro" expanding foam insulation just to name a few.
New home builders that combine tight construction methods with advanced insulation materials and follow proper moisture management techniques will have happy customers enjoying comfortable, sustainable homes with reduced utility costs.
I might share this opinion if I were a home heating fuel salesman, but as a Maine home builder with a focus on saving my customers money through energy efficient construction, I say that it is better to understand building science, specifically moisture management, and build new homes as tight as you are able.
Years ago, fuel costs were low, and moisture management not well understood. Houses that leaked air were not much of a concern. They would get wet, but with an abundance of air moving through the walls would dry avoiding moisture damaged assemblies.
With rising fuel costs houses had to become better insulated and tighter, and fortunately within the past decade or so, building science case studies have shown new home builders the way to build structures that are not only tight, but also properly manage bulk moisture from external sources and moisture vapor from internal sources.
Today's home builders are fortunate to have the availability of a wide variety of excellent building products as well as the educational resources to build new homes that are both energy efficient and sustainable.
Products such as "Greenguard Raindrop house wrap" which facilitates a drainage plane between exterior cladding and wall sheathing, "Advantech" brand roof and wall sheathing which is highly resistant to moisture damage, "DOW" "SIS Structural Insulated Sheathing", "Styrofoam" extruded insulation panels, and "Thermax" insulation panels, "DOW" "Weathermate" construction tape and "DOW" "Great Stuff Pro" expanding foam insulation just to name a few.
Wednesday, April 13, 2011
Fiber-Cement Siding: Worth considering for your new home

Available in horizontal lap, vertical panel, shakes, and trim, it is a green product known for durability and beauty.
A wide variety of factory applied finish colors are available which will remain beautiful long beyond that of a typical site applied finish product.

Proper installation techniques are critical when utilizing fiber-cement siding. A drainage plane should be incorporated into the wall system to assure that moisture can not be absorbed into the back side of the siding, and industry best practice techniques should be followed for flashing, sealing, and bulk moisture management.
As an added benefit, Fiber-Cement costs compare favorably to other available siding choices.
I look forward to exploring with you how Fiber-Cement siding could be a good consideration for your new home project.
Tuesday, March 22, 2011
Energy Efficient Wall Construction
There are many choices to consider when designing wall assemblies that will be energy efficient and provide homeowners with a comfortable home that is economical to heat.
But which is the best balance of performance and cost to build?
We have been utilizing a method that combines advanced framing techniques, insulated sheathing, diligent wall sealing, and high performance blown in insulation to achieve these goals, and are happy to see that in a Building Science comparison of high R-value wall assemblies, this method scored quite favorably.
The Building Science study can be viewed here:
Building Science.com/high-r-value-wall-assemblies
Additional details and construction photographs can be viewed here:
The wall system, balancing efficiency and cost.
We look forward to exploring with you how these construction methods could be the best choice for your new home construction project.
Building Science.com/high-r-value-wall-assemblies
Additional details and construction photographs can be viewed here:
The wall system, balancing efficiency and cost.
We look forward to exploring with you how these construction methods could be the best choice for your new home construction project.
Sunday, February 13, 2011
Radon resistant construction
A requirement of the new Maine Uniform Building and Energy Code (MUBEC) is Radon resistant construction techniques.
Radon, a soil gas that is prevalent throughout Maine has been linked to lung cancer.
We have previously partnered with the EPA to incorporate Radon resistant construction techniques in all new construction and believe that including it in the new building code was the right thing to do.
Many of the techniques were already included in our standard specifications, so it was fairly simple and inexpensive to comply with the remaining requirements and made sense to do so even before it became required by code.
An overview of the techniques follows:
Radon, a soil gas that is prevalent throughout Maine has been linked to lung cancer.
We have previously partnered with the EPA to incorporate Radon resistant construction techniques in all new construction and believe that including it in the new building code was the right thing to do.
Many of the techniques were already included in our standard specifications, so it was fairly simple and inexpensive to comply with the remaining requirements and made sense to do so even before it became required by code.
An overview of the techniques follows:
- Utilize perforated pipe for drainage/venting below basement concrete floor
- Back fill below basement concrete floor with clean gravel or crushed stone
- Utilize a poly vapor barrier above the gravel/stone and beneath basement concrete floor sealing the edges and penetrations with silicon caulk. Seal any foundation penetrations or cracks with silicon caulk
- Connect a PVC vent pipe to the below slab drain/vent piping and run vertically within the building enclosure and through the roof deck to vent soil gasses
- Add an electric outlet location in the attic space for a future vent fan if ever required
Together with appropriate building enclosure ventilation practices, these construction techniques will help assure homeowners of a healthy home living environment.
Thursday, January 13, 2011
New Energy Codes in Maine
In an effort to achieve conformity throughout the state, Maine has adopted the "Maine Uniform Building and Energy Code".
These new codes are now in effect in many cities and towns, and will be enacted statewide by July 1, 2012.
We welcome these new codes. We have always had a strong focus on energy efficiency and have typically exceeded code in an effort to achieve tight, well insulated houses that are easy to heat.
Some of the required changes however will add cost to a building project. As an example, foundation walls will now require continuous R-15 insulation, and concrete floors will require R-1o.
There are minimum U-Factor requirements for windows and skylights as well.
The following summary details the requirements by building enclosure element for Maine zone 6 ( all of Maine is zone 6 except Aroostook county which is zone 7).
Fenestration U-Factor: 0.35
Skylight U-Factor: 0.60
Ceiling R-Value: 49
Wood Frame Wall R-Value: 20 or 13+5(R-13 cavity insulation plus R-5 insulated sheathing)
Mass Wall R-Value: 15/19 (the second R-Value applies when more than half of the insulation is on the interior of the mass wall)
Floor R-Value: 30
Basement Wall R-Value: 15/19(R-15 continuous insulation on the interior or exterior, or R-19 cavity insulation on the interior)
Slab R-Value and Depth: 10, 4ft
Crawl Space Wall R-Value: 10/13
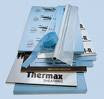
There are a number of strategies to achieve these new requirements. If you have questions about how these changes might effect your future project and which solutions will best balance performance and cost please contact me as I look forward to speaking with you further.
Subscribe to:
Posts (Atom)